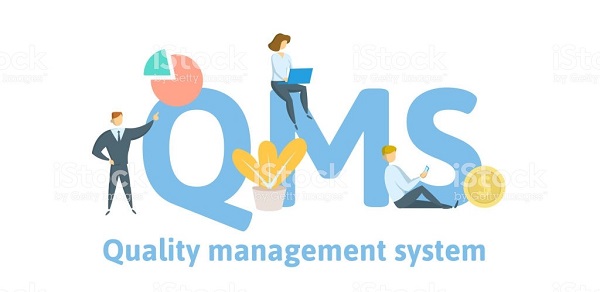
21 Jun Benefits Of QMS to Improve a Company’s Processes
Use your QMS to keep your company’s policies and procedures aligned with the launching and scaling of your products.
The digital age has changed the way we act, think and communicate. Yet, in so many cases the world of quality and compliance is still managed and indeed hampered by manual, paper-based systems. Quality management needs to move into the digital age. By modernizing legacy processes with an Electronic Quality Management System (eQMS) organizations can meet today’s quality challenges.
Quality Management Systems (QMS): Enable manufacturers to electronically monitor, manage and document their quality processes to help ensure that products are manufactured within tolerance, comply with all applicable standards and do not contain defects.
Quality Management System (QMS) software:
- Provides the procedures, processes, structure, and resources needed to streamline manufacturing and ERP operations while cost-effectively managing quality issues.
- As part of a closed-loop quality process proactively monitoring events across any enterprise source, effectively integrated Quality Management Systems (QMS) can identify potential problems before quality issues occur.
- Events may include supplier issues, manufacturing non conformances, complaints, services, and audits – both local and global.
- Provides the procedures, processes, structure, and resources needed to streamline manufacturing and ERP operations while cost-effectively managing quality issues.
- As part of a closed-loop quality process proactively monitoring events across any enterprise source, effectively integrated Quality Management Systems (QMS) can identify potential problems before quality issues occur.
- Events may include supplier issues, manufacturing non conformances, complaints, services, and audits – both local and global.
Benefits Of Quality Management Systems:
Implementing a quality management system affects every aspect of an organization’s performance.
Quality Management Systems (QMS) integrated with Manufacturing Execution Systems (MES) are strategic to a manufacturer’s business, providing complete visibility to manufacturing, field use and service information.
This knowledge helps to improve future product design efforts and to optimize production methods, allowing quicker ramp up in manufacturing.
As a result, manufacturers employing integrated Quality Management Systems (QMS) enjoy
- Decreased time to market,
- Real-time product risk evaluation,
- Minimization of recalls and negative brand exposure, and
- Lower per-product costs due to quality and process improvements as well as
- Decreased waste.
Additional benefits:
- Dramatic reduction of internal and external quality incidents
- Consistently higher-quality product output
- Significant reduction in the cost of quality operations
- A shift from problem detection to problem prevention
- Streamlined compliance with corporate and industry regulations
These benefits offer additional advantages, including:
- Defining, improving, and controlling processes
- Reducing waste
- Facilitating and identifying training opportunities
- Engaging staff
- Setting organization-wide direction
- Communicating a readiness to produce consistent results
Quality Management Systems (QMS) Capabilities and Outcomes:
Capabilities offered by Quality Management Systems (QMS) include:
- Global visibility across distributed operations
- Enforcement of process to ensure compliance
- Event monitoring and early trend escalation
- Global risk management
- Automatic containment of suspect items
- Intelligent root-cause analysis
- Automated quality assurance
- Adaptable best practices
- Enterprise scalability
How do different business functions benefit from using QMS?
While the importance of QMS has traditionally been as a quality, audit and risk tool, some of the biggest gains come in other areas, such as leadership, customer service, sales and marketing, procurement, and HR. This has led to many organizations dropping the word ‘quality’ from ‘QMS’ and rebranding it as the business management system.
Element And Requirements Of A QMS:
Each element of a quality management system helps achieve the overall goals of meeting the customers’ and organization’s requirements. Quality management systems should address an organization’s unique needs; however, the elements all systems have in common include:
- The organization’s quality policy and quality objectives
- Quality manual
- Procedures, instructions, and records
- Data management
- Internal processes
- Customer satisfaction from product quality
- Improvement opportunities
- Quality analysis
Establishing And Implementing A QMS:
Before establishing a quality management system, your organization must identify and manage various connected, multi-functional processes to help ensure customer satisfaction. The QMS design should be influenced by the organization’s varying objectives, needs, and products and services provided. This structure is based largely on the plan-do-check-act (PDCA) cycle and allows for continuous improvement to both the product and the QMS. The basic steps to implementing a quality management system are as follows:
- Design
- Build
- Deploy
- Control
- Measure
- Review
- Improve
Meeting the customer’s requirements, which helps to instill confidence in the organization, in turn leading to more customers, more sales, and more repeat business
Meeting the organization’s requirements, which ensures compliance with regulations and provision of products and services in the most cost- and resource-efficient manner, creating room for expansion, growth, and profit
The purpose of QMS is to ensure that, every time a process is performed, the same information, methods, skills and controls are used and applied in a consistent manner.
A QMS organizes this information to give each person access to their own custom to-do list. Permissions control who sees what and when. Overall, a QMS delivers a complete record of business processes, so you can better understand improvement initiatives.
Atachi QMS has an in built intelligence to capture documents processes, procedures, and responsibilities for achieving quality policies with strict adherence to GMP (Good Manufacturing Practices) and objectives of an organization.To learn more about Atachi QMS click here.